Being Transparent! Here’s How Your Custom Boxes Are Manufactured!
2022-10-04 11:15:17
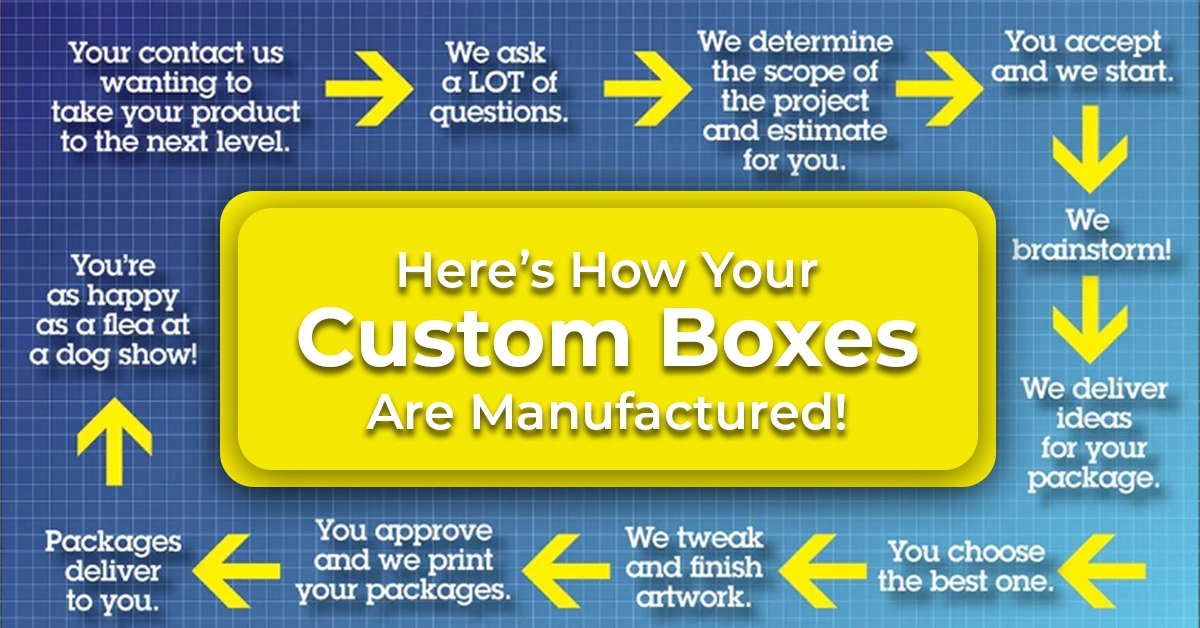
Have you Ever Been Curious About the Manufacturing Process of your Custom Boxes? If yes, then the good news is that the future belongs to the curious. So, firstly, congratulations on being a part of the future. But, enough with all the pep talk. Because today, we’re going to let you in on our secret. And we hope you will keep it safe with you.
You Often Experience Hesitation When Making your First Order, Right?
The primary reason is that you don't know how the company works. So, today’s writing is a quick fix to help you overcome all of your doubts and hesitations. Are you ready to take an inside look at how we work? From the placement of your order to its delivery, we have got it all penned for you.
So, without any further ado, let’s get the dice rolling!
1. Contact Us (or, to put it another way, Touch Base With Us)
Typically, the first step in placing an order is communicating with the support staff. So, let's see how you can talk to us.
- The First simple and easy method to talk to us is through our “Live Chat Support.” You can see the icon at the bottom right corner of your screen.
- Secondly, you can leave us an email at “sales@oxopackaging.com".
- Thirdly, if you want to talk to us directly, call us at (510) 500-9533.
2. Information We Need
Now, what will we talk about? Obviously, not about the latest fashion trends. Because we understand that you’re hustling with your work. And time is money. So, we really don’t want you to waste it. First and foremost, we want you to share the following job specification for your custom boxes with us.
i |
Dimensions |
ii |
Quantity |
iii |
Material |
iv |
Color |
v |
Box Style |
Dimensions
Dimension is the crowning factor in Custom Packaging. The safety of your product can only be maximized with precise dimensions.
Moreover, the right box dimensions are important to provide a sturdy fit to your product. That’s why it's the first thing our staff will ask from you. We request that you share with us the accurate dimensions of your box, keeping in mind the following aspects.
1. |
Length |
2. |
Width |
3. |
Height |
You can share your product's dimensions with us if you're unsure of the box size. And in due course, our Packaging Expert will figure out the ideal box dimensions.
Quantity
This is another important aspect that needs to be taken care of. Your box quantity, among other aspects, helps our estimation department come up with a price quote for you. We'd like to tell you something that we know you'll find fascinating. Your maximum order quantity will get you the minimum rate. Now, isn’t that interesting?
Minimum Quantity Order |
50-100 Boxes |
Materials
Our material screams the word "quality." And you need to take our word for this. Sustainability is one of the many factors that can be guaranteed with our Custom Boxes. Most of our clients are indecisive about the material selection. But no need to worry. Because once you have shared your product details with us, you’re all set.
If you’re not sure about the material - our experts can recommend it to you. Only after considering the following factors.
- The weight of your product.
- The style you want to go with
- Your order expectations.
1. |
Cardboard |
2. |
Kraft |
3. |
Rigid |
4. |
Corrugated |
1) Cardboard
Cardboard is an all-rounder!
- It is one of the most commonly used packaging materials.
- It offers the maximum protection for your product.
- It is durable and cost-efficient.
Cardboard stock is perfectly suitable for the following product categories.
- Cosmetic Items
- Hygiene Products
- Cigarettes
- Vape Products
- Cereal or Food Items
Here are a few box styles made up of cardboard. These boxes have proven to be a marketing extension for various businesses.
- Custom Retail Boxes
- Custom Soap Boxes
- Custom Candle Boxes
2) Kraft
100% Recyclable!
Yes, we’re talking about kraft stock.
- It is extraordinarily strong.
- It conveys a positive brand image.
- Most importantly, kraft is highly moisture resistant.
Here are a few products that can be accommodated in Kraft Boxes.
- Jewelry Items
- Bakery Products
- Gift Items
- Soaps
- Makeup Products
Kraft Paper is also referred to as carbon or brown paper. And this often leads to the misconception that kraft is only available in brown color. You can order your Customized Kraft Boxes in any color of your choice.
Some of our best-selling kraft boxes include:
- Custom Kraft Pillow Boxes
- Custom Kraft Soap Boxes
- Custom Kraft Display Boxes
3) Rigid
If the word luxury had a second name, we would have named it rigid.
- Rigid is a premium material.
- Rigid can best handle your delicate items.
- It has a strong, robust nature.
You can use rigid boxes for the following products.
- Board Games
- Books
- Jewelry Items
- Perfumes
- Wrist Watches
A few of our very successful rigid packages include.
- Custom Rigid Jewellery Boxes
- Custom Luxury Rigid Boxes
- Custom White Lable Pre-roll Boxes
4) Corrugated
Did someone say corrugated? But, we heard about shipping! How uncanny!
Corrugated is your ultimate shipping material
- It is supremely dense.
- It is resistant to both water and weather.
- It is used to pack all heavy-duty products.
Corrugated boxes can be a perfect fit for the following products.
- Cereals
- Fast-food
- Electronic Supplies
- Glass-made Items
- Office Supplies
Some of our most popular corrugated packaging include.
- Custom Pillow Corrugated Boxes
- Custom Pizza Corrugated Boxes
- Custom Mug Corrugated Boxes
Color
More than 80% of consumers are drawn to a product by its color. Now that is a crazy number, right? Do you know that color can trigger and evoke feelings in us? We help you put this theory to best use with our color printing alternatives. At OXO Packaging, we can work with as many colors as you would like. Here are your color printing choices.
1. |
One Color Printing |
2. |
Two Color Printing |
3. |
Full-Color Printing ( Three or More Colors) |
Box Style
Surprise your customers with the perfect box style! Your box style can become a trademark of your product.
Some very common but Trendy Box Styles include
1. |
Tuck Box |
2. |
Mailer Box |
3. |
Gable Box |
4. |
Sleeve and Tray Box |
5. |
Top and Bottom Box |
These are only a few of the style options. To find out more, you can visit our website.
3. Estimation and Getting your Quote Ready!
Once you share with us the aforementioned details, our estimation department starts working on giving you the best quote possible.
Since every job is variable, a client sometimes requests special add-ons, with absolute finishing features, therefore we have to struggle to make the prices as economical for you as possible. Here, the sales agent working on your job consults with the estimation department. The details estimation team requires to produce the best quote are...
Dimensions of the Box
- The nature of the packaging material (Cardboard, Kraft, Rigid Stock, Corrugated)
- Color requirements (single color, double color, full-color printing, CMYK)
- Quantity of the custom boxes required
Once your sales representative provides all the input, the estimation team, within an hour, prepares a quote for you. The quote includes the price per box and the total amount for the entire job in United States dollars (USD). Since we provide discounts on bulk orders, therefore we work as diligently as possible to place a discounted price on the table for you.
Hear Out the Best Prices within an Hour!
We strive to provide you with the best experience with a fast and effective process. The maximum time we need to prepare a quote is one hour, but don’t think that you have to wait for that long. In fact, the only time it requires to produce a quote is the time our sales agent needs to consult with the estimation department and the further calculation they do at their end.
Surprisingly, sometimes it is not more than 30 minutes. As soon as we are done with the estimation, we forward you the prices in detail via email.
The agent also makes a call to let you know about the pricing in detail. We love to hear from you about what works for you. If it is in your best interest then we can negotiate on the pricing without compromising an iota on the quality of your Custom Packaging Boxes.
4. The Design Process
So, you were here for the Custom Boxes for your product. Right. We started from box dimensions, discussing the materials, your preferred color and printing choice, and the quantity you need.
Now you Have the Estimated Quote from Us. What’s Next?
Well!! OXO Packaging works the same as any other business. Yesterday morning I had this strange craving for molten lava cakes. The craving took me to the bakery shop at the street’s corner. I can’t believe I could become that impulsive. As soon as I found myself in the shop, I ordered a medium-sized molten lava cake.
Ms. Darcy who always wears a pretty smile on her face said $23 and without a second thought, I paid and grabbed the cake I desired the most.
You heard from us. You have the quote in hand. It's your take now! If you want to discuss the pricing, our sales agent is always here for you. If the pricing works for you then we move towards the next step which is the design phase. The design process is the most mirthful one and gives us enough room to leave a mark on customers.
We have a bunch of aficionados i.e. designers that are ready to get you onboard to give you a packaging design in which you find solace. So, what happens next? The estimation is done. A quote for your order is prepared. The pricing works for you. Now the design phase starts. This stage begins with asking two fundamental questions.
You Have the Design! Bravo
The first thing we ask clients once we initiate the discussion about design is whether or not they have the design in hand that they want to print on their preferred boxes. If they have the design, we then prepare a mockup for them. The 2D mockup is in fact the first digital image of their box that we prepared with their design printed on the box.
You Don't Have the Design? Here’s Our Complimentary Design Services
The design process described above is only possible when you provide us with the specific design requirements. Wait...
What if you are blank about the design? What if you don't have one in mind but need boxes on an urgent basis as your product is anxiously waiting to flourish in the market? OXO Packaging provides free design consultation services. In this process, our expert designing team understands and listens to you very carefully.
We begin with the box size, then we discuss the colors, the illustrations, any sorts of visuals, and all other minor details that make a design worth having.
OXO Packaging Custom Design Features
With extensive experience, our team has the experience required to create the perfect Custom Packaging Box. We design the perfect box for you according to your requirements. We can share templates to give you a better idea of our packaging.
We offer the best design services. Some features of our Custom Box Design include.
Custom Printing
One of the most essential parts of a Custom Box is printing. The printing should be perfect to create a seamless design. We pay a lot of attention to the printing of your Custom Box. We make sure that there is no flaw in it. If the printing is great, that means 70% of the work is perfect.
Always The Right Colors
Another essential part that requires focus is the colors you choose. Sometimes during the printing process, the color changes from the original and your Custom Packaging comes out in multiple different shades of the same color. We don’t let that happen on our watch. We make sure that the colors stay as you provide us.
Premium Add-Ons To Highlight Your Brand
We offer premium add-ons to make captivating Custom Printed Boxes. Nowadays, every brand wants to create a unique identity.
Everyone wants to be perceived differently, and the same goes for retail products. For that purpose, Custom Packaging is probably the best haven. But when we specify things a bit, in the end, these are the minor details and add-ons that draw the line between a good Custom Box and a seemingly average box.
Here at OXO Packaging, we offer numerous add-ons to glorify the beauty of your Custom Packaging. See the list for more details.
- Lamination (Gloss/ Matte/ Spot UV)
- Embossing
- Debossing
- Inserts
- Gold Foiling
- Tear Strips
- Holographic & Pigment Foiling
Your Design is Ready. Cheers!
Once the work on your design completes, the designing department sends it to your respective sales agent. Our sales representatives are the gateway that unlocks your connection with the Custom Packaging Boxes for your product. At every stage, the sales staff make sure that you get value for your time, attention, and money.
Once the design is sent back to you we also send you the payment invoice based on the price you agreed on earlier. In this step, we again confirm the quantity you require in case of a change of one’s mind and an invoice is generated. Once you pay for your order, we then wait for the design confirmation from your end.
Getting Your Approval
Once the design is complete, we then send the design to you for approval. This is the final approval phase. You can check the final design and suggest changes if you find anything missing. We can provide a 3D mockup of the design upon request. If there are no changes required, your product goes over to the next phase which is the production of your Custom Boxes.
So, let’s move on to the production phase and see what happens there.
5. The Production Phase
This is where the real magic happens. All your requirements, including your choice of material, the shape of the box, the design, and every small detail, are sent over to the production department. OXO’s production department brings your design out of the computer screen and into the real world. Our Custom Boxes production phase has 3 steps. These are;
- Printing
- Cutting
- Finishing
Here’s how it all flows;
Printing
In the first step, your design is printed on your preferred material. For example, if you want a Cardboard Box, we print your design on big sheets of cardboard. These sheets then move on to the next step.
Cutting
This is the step where your boxes first get their shape. In this step, the printed sheets from step 1 are cut into boxes. After the cutting is done, you can see what your boxes look like.
Finishing
This is the final step in the production phase and may be the most important one. In this phase, your boxes receive all the finishing touches. The edges are refined, folds are defined, and the boxes get their final shape.
We also apply the add-ons that you select in this phase. For example, if you want your logo embossed on your box, this is the step where it is done. After finishing the production process is complete. We have explained our production phase completely. So now, let’s move towards the next phase in our process of making Custom Boxes for you.
6. The Quality Assurance Phase
This is the most necessary phase in our whole process. In this phase, our quality assurance team makes sure that the product is ready to be shipped. In this phase, our team checks for any issues with your boxes. Whether that be the printing, shape, color, or any other issues. Each box from the lot is checked to see if it fits the quality expectations of the client.
This phase makes it possible for us to deliver the right product to you. Client satisfaction is our number one priority so we make sure we do it right the first time.
The Things We Check
There are a lot of factors that make up the box. All these factors are individually checked to make sure the quality of your boxes is right. The main things that our QA team checks for in a box include;
- Colors - to make sure that you receive the right shade that you selected.
- Printing Errors - text, patterns, design, and everything else in printing are checked.
- Finishing of the boxes - making sure that the finish is right and the box shape is perfect.
There are other factors involved in our QA phase but these are the main issues we check. These issues are the most common issues that you see in custom box printing. So, we make sure that these issues are resolved first.
What if The Boxes Have Issues?
If our QA team finds boxes that do not fit the quality standards (which happens very rarely), these boxes are rejected and new ones are printed. We do not deliver your product unless each box passes the quality assurance phase. Once our QA team approves the product, it is ready to be shipped.
7. Shipping - Your Order Is On The Way!
After going through all these phases, your Custom Boxes are finally ready to be shipped. We get your order shipping-ready by packing it properly so nothing gets damaged during shipping. After we have shipped your product, we provide you with a tracking ID. You can easily track the status of your delivery using that ID.
How Long Does it Take?
The whole process along with the shipping takes around 15 business days. From manufacturing to delivery and you receiving the product, it takes around two weeks. But the final Customized packaging that you receive is worth the wait!
The Final Phase
The process isn’t concluded when your Custom Boxes have been shipped. Our process ends with your satisfaction. Once you receive the order, we ask for feedback. If you are satisfied with the order, only then is the order complete. When working with OXO Packaging, you have nothing to worry about. Client satisfaction is our first priority and we do everything for it.