A Guide to Optimizing the Packaging Cost and Logistics
Salman Shahid 2025-03-11 11:13:26
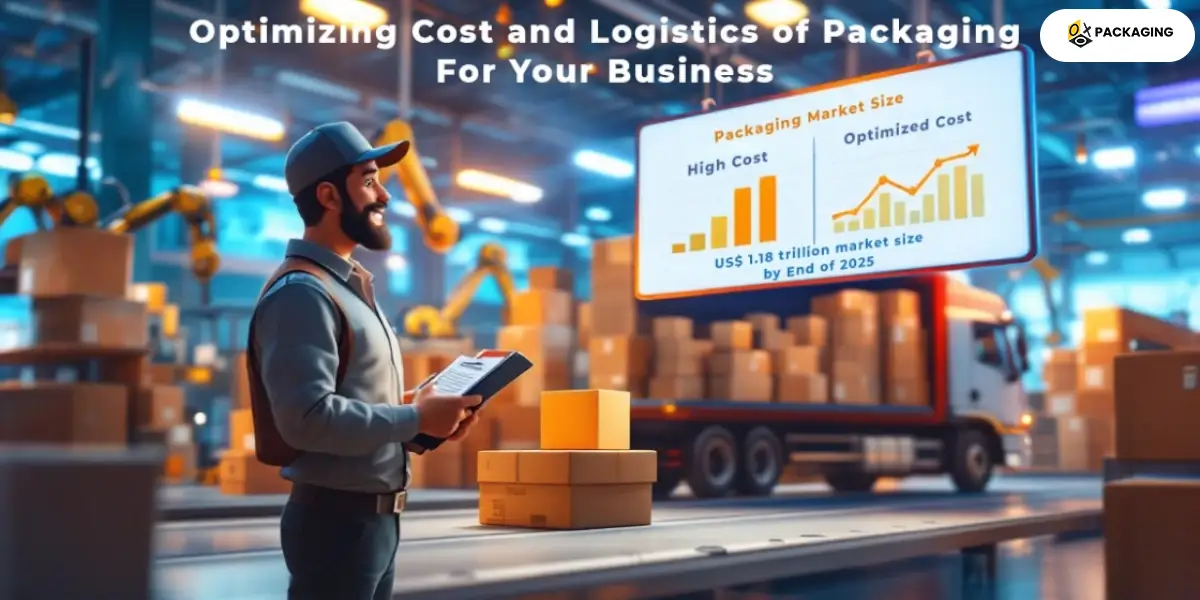
Keeping the cost minimal and streamlining the supply chain is essential yet difficult when it comes to product packaging. According to Mordor Intelligence,
“The packaging market size is estimated to reach around US$ 1.18 trillion by the end of 2025.”
Such a large market volume comes with huge costs and logistical problems for businesses. Overcoming these challenges and finding convenient ways to streamline the overall operations of your business is essential.
Let’s help you with that! In this blog, we will dive into a detailed guide on optimizing the cost and logistics of packaging for startups as well as established enterprises. Read on!
What is Packaging Logistics?
Packaging logistics is the process that covers manufacturing, shipping, storage, and usage of product packaging. It also included the process of packing products for retail purposes.
Optimizing the logistics in packaging is essential for retail businesses to streamline the supply chain and ensure efficient order fulfillment. Optimized logistics assist in supply chain management that makes the process of manufacturing, packing, and selling goods easier.
To do so, understand the fundamentals of packaging logistics, and opt for the best practices accordingly that suit your needs. Here are 4 logistics fundamentals of packaging you must know:
-
Manufacturing
Logistics of packaging begins with its manufacturing. This process includes deciding the material and getting tools and machinery for production purposes. Many raw materials types are out there to make robust packaging for your goods.
You can choose from paper and plastic to metal and glass materials to make product boxes and bags. After the selection of materials, the next process is sourcing equipment and machinery to shape and print packaging. The machinery you choose depends upon your specific manufacturing requirements as well as the material you use to make packaging.
For instance, you can use the die-cutting process to shape plastic or paper-based materials. However, the die-cut machine can’t be used to cut glass or metals.
-
Shipping And Product Packing
After manufacturing the product packaging, the next step is shipping it to packing units. Shipping requires significant care so that the packaging doesn’t get damaged due to knocks during transit. If you are delivering cardboard boxes or corrugated packaging boxes to packaging units, tying them with durable ropes is essential. Doing so will keep your boxes in place throughout the transit.
Packaging packing or packaging units have a great role in optimizing the logistics of your product packaging. Once your packaging is delivered to these units, packing of products begins. To do so, manual and automated systems can be used depending on your specific requirements.
-
Warehousing of Packed Products
Planning the storage of packed goods is also an important part of optimizing packaging logistics. Warehousing helps store inventory manageably in a specific space. Choose the space that shelters your goods but also stacks your items suitably to occupy less room, leaving space for mobility.
When considering spaces for your inventory, consider the ideal environment for your products. Some items need to be stored with care at certain temperatures. Make sure your warehouse has appropriate facilities to keep your products pristine till they are moved to retail markets to be delivered to end consumers.
-
Distribution to Retail & Fulfillment Centers
Distributing packed goods to retail stores and direct-to-customer (DTC) brands is the final step to cap your supply chain. You can benefit from third-party logistics (3PL) or do it yourself. To resonate the market demand with your manufactured product quantity, keep the load minimal to warehouses.
Maximum of your goods should be in the retail stores or fulfillment centers (in the case of e-commerce businesses).
3 Types of Product Packaging in Logistics
Now that we know the fundamentals of logistics packaging, let’s explore some types of product packaging. Here are 3 types of packaging categorized based on their logistical significance:
-
Primary, or Consumption-Unit Packaging
Packaging that comes in direct contact with the products is known as primary packaging also known as consumption-unit packaging. The prime purpose of this type of packaging is to provide the first line of defense for the products. Also, primary packaging is used to showcase your brand identity.
You can print whatever you want on this packaging type to boost your brand and fascinate your target audience. Primary packaging mostly comes in the form of mylar or plastic bags, kraft paper bags, or
-
Secondary, or Grouped Packaging
Product packaging that accumulates several products is called secondary packaging. This type of packaging does not come in direct contact with the products, yet provides significant protection to the goods packed in them.
This packaging for retail products is suitable for delivering items directly to customers or showcasing these products on retail shelves. The importance of secondary packaging can't be overlooked when it comes to managing retail logistics. The reason is that this packaging is designed to pack products in a portion that most of the buyers demand.
-
Tertiary Packaging
When it comes to safe shipping of large inventory from manufacturing units to warehouses, or directly to retail stores, tertiary packaging is used. Corrugated shipping boxes are often used as tertiary packaging in the market.
The reason is that these boxes are not only robust but also offer a cushioning effect to protect goods during transit.
How to Streamline Operations of Packaging Logistics?
Streamlining operations of packaging logistics helps you improve supply chain management, but how can you do so? Here are some easy tips that can help you optimize your packaging logistics with a breeze:
-
Standardized Packaging Measurements and Quality
Quality control and standardized measurements play an important role in streamlining your packaging logistics. The packaging measurements can be standardized based on the portion or dimensions of products that you want to pack inside.
And when it comes to packaging quality, create a checklist that doesn't miss any aspect you need to verify before finalizing the quality.
Quality Control Checklist
- Packaging material meets product specifications
- Packaging durability and sealing
- Visual defects or damages
- Correct labeling (item number, product description, expiry date, etc.)
- Including COCs if required
- Secure shipping of product packaging
-
Automation of Packaging for Selection and Handling
Packaging automation not only streamlines the process but also helps reduce the effort and cost of the packaging process. You can benefit from the automation machines and processes that pack products without the need for manual assistance.
To do so, you can explore this 4 step-guide on packaging automation:
Prepare Automation Facility in 4-Step
- Equipment Selection: Choose reliable and long-lasting machines that smoothly carry out the process. You would need robotic palletizers, cartoning machines, labeling machines, and filling machines.
- Preparing Site for Selection: This process involves making appropriate changes to implant machinery and optimizing space ergonomics to support the workforce.
- Installation: Implanting and installing the equipment in the workspace such that it is easy to operate is necessary.
- Training of Workforce: The last step is training your workforce such that the workers can conveniently use the machinery and do their tasks without hassle in the workplace.
-
Ergonomic Optimization of Packaging Units & Warehouses
Optimizing the workspace where packaging is manufactured or used such that workers can easily perform their duties is essential. Paying attention to the ergonomics of the workplace not only provides workers with ease but also boosts up the overall process and ultimately performance.
Here is an ergonomic checklist you can use to optimize packaging units and warehouse spaces:
Ergonomics Checklist for Packaging Units
- Avoid excessive exertion of the workforce due to machine design.
- Avoid machine design that causes workers to stand or sit in faulty postures.
- Optimize space to create room for both workers and machines.
- Keep the distance between the operator and the machine optimal.
- Provide technical manuals for the machine operator.
Calculating Cost of Packaging
When it comes to improving the profit with minimal investment, reducing the cost of operations matters a lot. For your retail business, you can optimize packaging costs such that you can stick to your budget while meeting your packaging needs.
Reducing the cost is important if you want to get maximum benefits without investing much. Here are some important factors that you can control to minimize the cost of product packaging:
-
Material
Packaging material is one of the primary determinants of packaging cost. Choose the packaging material based on your packaging needs. If you can pack products in low-budget packaging, prefer not to invest in costly packaging material.
For instance, if you are a jewelry brand looking for luxurious yet inexpensive packaging, go for double-wall cardboard boxes instead of rigid boxes. Cardstock boxes are excellent for lightweight jewelry products like necklaces, bracelets, etc., and exude a luxurious vibe.
-
Customization & Printing
Customization is one of the major determinants of packaging cost. The more customizations you choose for your product packaging, the more the cost will increase. For example, plain boxes and bags will cost you less than printed ones and those with custom inserts.
-
Quantity
The quantity of packaging also determines the overall cost. Certainly, 100 boxes will cost you more than 100 packaging boxes. However, many packaging suppliers like OXO Packaging offer wholesale discounts for bulk quantities. That’s how they help you save price per piece.
-
Storage Cost
Storage of packed products also has its cost. The rent of warehouses or 3PL companies may add to your business operation budget if you overproduce your goods. One of the best ways to cut storage costs is choosing just-in-time manufacturing approaches.
The Average Costs of Packaging in Businesses
Knowing the average cost of product packaging gives you insight into which type of packaging will meet your needs and fit your budget as well. Here are some average prices of product packaging based on their material along with the application of packaging materials:
- Corrugated Packaging: $2.7-$3.5. This packaging is mostly used for mailing and shipping purposes.
- Folding carton: $1.8-$2.25. These cartons can be used for retail packaging along with mailing purposes.
- Rigid boxes: $8.5-$10.00. These boxes are used to pack premium and luxurious products like jewelry, cosmetics, perfumes, etc.
- Custom mylar bags: $1.79 to $4.99. These bags are mostly used to pack processed foods like chips, powdered milk, sauces, etc.
- Glass beverage bottles: $2 to $4. Various types of glass packaging are available depending on their usage. However, bottles for beverages pack juices, soft drinks, alcohol, etc.
The cost of packaging not only depends upon the packaging material; it also depends on the packaging customizations. For instance, a plain cardboard box with no printing may cost you around 1$ per piece. On the other hand, printed cardstock boxes with printed graphics and die-cut windows will cost you more than $2.
Cost Management in Packaging Production
If you want to manage the cost of packaging production, you also need to look into the supply chain challenges. Overcoming these challenges will help you secure good profit like it did for Star Buck in 2009.
Case Study: In 2007 & 2008, the unwanted rise of the $75 million cost of the supply chain got the attention of Star Buck’s executive team. The challenge was to optimize the supply chain to reduce the cost and maximize the profit. To overcome this challenge, the reorganized supply chain, reduced cost to serve, and improved production facilities. Doing so, helped them secure more than $500 million in 2009 and & 2010.
Tax Considerations for Packaging
Managing deductible packaging expenses is also essential for businesses to calculate the exact profit of their businesses. If you want to get the maximum out of the minimum investment, efficient tax planning strategies are paramount.
When it comes to packaging taxes, primary and secondary packaging are exempt from any taxes in most states of the USA. However, using commercial shipping packaging boxes for moving or tertiary packaging makes your business liable to pay tax in Arvadaco and other states.
The amount of tax varies from one packaging to another depending on the material, measurements, and thickness of the packaging.
4 Ways to Reduce Packaging Costs
Now we have discussed in detail the cost of packaging, but how can we reduce it to get maximum profit? Here are 4 simple ways you can reduce the packaging cost of your business:
-
Just-in-Time Manufacturing
Just-in-time manufacturing means producing the goods in a quantity that can be easily sold within no time. To establish such a system, you need to understand the market demand and design the supply chain accordingly.
You can benefit from AI to comprehend real-time customer behavior and fluctuations in market demand to carry out just-in-time manufacturing efficiently. Streamlining the manufacturing in such a convenient way reduces storage costs and minimizes the chances of product waste.
-
Using AI-Powered Automation to Reduce Packaging Waste
Packaging waste is one of the primary factors that adds to packaging costs in a supply chain. Reducing waste is to the maximum extent essential if you want to minimize your business cost and get maximum profit.
You can benefit from AI-powered automation machines that use LLMs to comprehend the personalized packaging needs of your products. Such innovative machinery ensures only the material that is needed is used for packaging.
-
Ensuring the Quality of Packaging to Minimize Returns
Customer satisfaction is the priority when it comes to boosting your sales. Even if your product is in good shape, damaged packaging may result in returns. So, if you want to minimize the losses due to order returns, pay attention to the durability of your product packaging.
To do so, you can benefit from durable packaging materials that don’t tear during transit. Also, added protections like cushioning inserts also help keep products pristine minimizing damages and ultimately reducing returns.
-
Stay Ahead of the Curve With Packaging Innovations
It’s not always about reducing the cost; maximizing profit matters more. Stay informed about the innovative packaging trends and design your business operations accordingly.
For instance, more than 80% of customers prefer to buy products packed in sustainable packaging. Considering this fact, you can go for compostable and biodegradable plastic alternatives for your packaging like seaweed and starch-based packaging.
Using compact robotics for error-free packing, sorting, and handling in a limited workspace is also ideal for saving costs. You can use smart packaging features like QR codes and sensors to track various aspects of the supply chain that help minimize losses and boost profit.
Outsource Product Packaging to Industry Experts!
Managing packaging logistics and keeping the packaging cost low is prolific yet challenging. An easy way to optimize your packaging operations without investing much is outsourcing the packaging of your business. To do so, you can rely on online packaging companies offering you complete material, size, and design support.
OXO Packaging, for instance, is your reliable packaging partner in the USA offering endless customizations for your packaging. Reach out to us today and find an excellent packaging solution for your business at a wholesale price.
Final Words!
Managing the logistics of packaging and saving on packaging costs are crucial to retail businesses. We hope now you know how you can manage packaging logistics and optimize costs to get maximum profit. If you still have questions or want to buy packaging for your business, reach out to us today!