Functions, Applications and Comparison between Matte and Gloss Lamination
2022-04-27 10:24:55
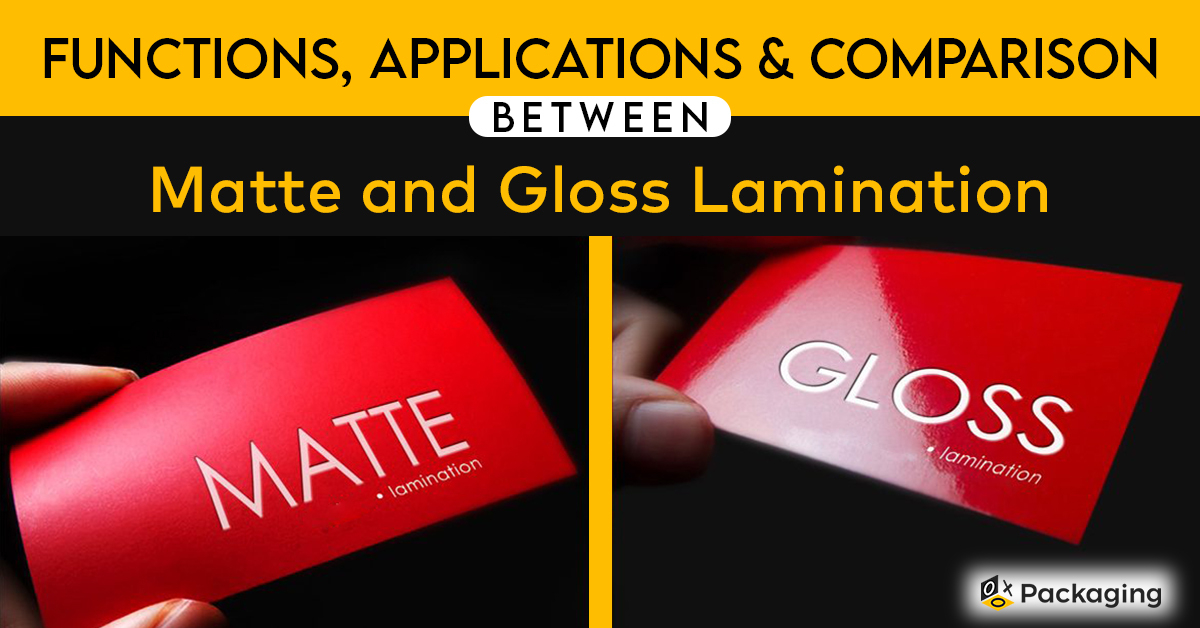
Lamination is a process through which the packaging surface is enhanced by mixing flexible packaging bands together. Generally, lamination is a technique through which a manufacturing material is made in multiple layers to achieve higher stability, strength, and shine. In the packaging industry, the common lamination types are matte and gloss. Even though plastic lamination was also highly common in the packaging context, the material is no longer preferred as a laminating agent due to its persistence. It protects the printing pieces from getting dirty, fragile and dull.
Moreover, lamination is also reliable in protecting the printing pieces from moisture, scratches and stains. Lamination makes the surface of the Kraft paper stain free as it acts as an extra protective and shiny layer. The applications of laminations are wide-ranged. As mentioned earlier, the types of lamination are diverse, with each lamination type serving a unique purpose. Besides matte, gloss and plastic lamination, bagasse lamination is also highly popular. This lamination type is extracted from sugarcane bagasse and is considered the most environmentally friendly lamination.
Applications of Lamination
Lamination can be used for magnifying the outlook of a variety of items. These are applied on,
- Custom packaging boxes for grocery, cosmetics, jewelry, and food as laminations help in branding.
- Restaurant menus to make them shiny, stain-free and luxurious.
- Rigid boxes for jewelry are also laminated with matte that provides a soft velvety touch to the box's surface.
- Food packaging is also commonly laminated with plastic, adding an extra protective layer. This lamination keeps the food content in place and assists in long-distance shipping.
- Book printing papers and business cards are also laminated with gloss. It makes the surface look new and keeps it neat at the same time.
- Maps and documents are also laminated with hard stock plastic. This lamination is solely done to keep the sensitive document safe from stains.
Why is Gloss Lamination so Demanding?
Gloss lamination reflects the incoming light, thereby making the surface of the Custom Printed Packaging Boxes shiny and lustrous. Compared with matte lamination, gloss is cheap; however, the big hurdle is that most packaging retailers don't clearly understand when to use gloss lamination. The demand for gloss in the custom packaging increases as it provides branding benefits.
When to Apply Gloss Lamination?
- Apply the gloss lamination when you want to make the printed contents on the packaging boxes clearly readable. Gloss increases the text's visibility and provides a valuable purchasing experience to customers.
- Gloss lamination is also remarkable if you are interested in logo branding. For example, on custom CBD boxes, if the logo is printed right at the centre, then gloss lamination can increase its visibility. In this way, customers can quickly identify a product because its logo is prominent to their eyeballs.
What is Matte Lamination?
If you are more like a shopaholic person, I can presume that you have touched some boxes with soft velvet-like surfaces at least once in your life. Matte lamination provides a smooth, silky, and velvety texture to custom ring boxes and other products. This lamination type is known primarily for providing a luxurious experience to customers. Compared to gloss lamination, matte is expensive since this material is rare. Moreover, light does not reflect from the surface of matte lamination. It is also known as 'soft touch' as fingerprints are less visible on its surface.
When to use Matte Lamination?
- Apply the matte lamination when the printing colors are gloomy. It makes the surface softer and magnifies its outlook.
- If you are interested in providing a sophisticated yet modern look to your custom boxes of cards, then make matte lamination your perfect companion.
- Apply this lamination to the boxes of printing pieces that are not used regularly. In this case, the best choices are Luxury Jewelry Boxes, cardboard boxes and other products. These boxes are used only for material handling and placed once the product is used.
- Moreover, put matte on all sorts of printing packaging boxes. Even if used regularly, it can get high scratches and smudges.
Matte V Gloss: A Quick Comparison
Both the matte and gloss laminations are unique in their use cases. However, there are certain factors on which their pros and cons can be assessed.
Conclusion
Both the matte and gloss are unique in their applications. Their functions differ from each other however, when applied together the result these lamination provide are extraordinary. It is therefore projected that in future, the laminations will play a major role in determining the quality of a product as these are the enticing and branding friendly features of the custom packaging of any product.